Die Entfernung der Schaumschicht aus der Schaumflotation ist nach den Entwurfskriterien eine mutige Aussage. Die Tatsache, dass ein solches Gerät nicht nur existiert, sondern über 50 Betriebsinstallationen verfügt, zeugt vom Druck auf die Industrie, angesichts moderner Herausforderungen neue Lösungen zu finden. Niedrige Gehalte, komplexe Erze und steigende Energiekosten haben zur Entwicklung völlig neuer Flotationsgefäße, zur Verbesserung bestehender Technologien und zu neuen Überlegungen zu Flotationsflussdiagrammen geführt.
Das schaumfreie Flotationsgefäß stammt von der Eriez Flotation Division, die es 2002 patentieren ließ und unter dem Namen HydroFloat vermarktete. Es ist speziell für ein innovatives Flussdiagramm gedacht, das eines der größten Probleme des Bergbaus angeht: Mit mehr zu verarbeitenden Tonnagen und feinkörnigerem Erz erfordert die Zerkleinerung immer mehr Energie. Wenn Flotationskreisläufe gröbere Partikel verarbeiten könnten, könnte Energie im Zerkleinerungskreislauf eingespart werden.
„Die meisten Bergbauunternehmen haben es mit sinkenden Erzgehalten und komplexer Mineralogie zu tun“, sagte Barun Gorain, Direktor der Strategic Technology Solutions Group von Barrick Gold. „Das eigentliche Problem ist, dass mehr als 99 Prozent dessen, was wir tatsächlich in der Goldindustrie abbauen, als Abfall gelten.“ Er sagte, dass die Grobpartikelflotation es den Minen ermöglichen könnte, Abfälle früher in der Wertschöpfungskette zurückzuweisen, was dazu beitragen wird, die Kapital- und Betriebskosten zu senken.
Leider erreicht die herkömmliche Flotationszelle nur in begrenzten Größenbereichen eine hohe Rückgewinnung. Zum Beispiel könnte ein Sulfiderz bei 90 bis 120 Mikron sehr gut schwimmen, aber nicht bei 50 oder 150 Mikron.
Die bisherige Forschung hat zwei Hauptgründe für die Obergrenze für schwimmfähige Partikelgrößen identifiziert. Erstens neigen gröbere Partikel dazu, nicht so viel Oberflächenmineralisierung zu haben, um Blasen anzuziehen.
Zweitens neigen sie dazu, sich wieder zu lösen, selbst wenn sie sich anhängen können. Bei den meisten herkömmlichen Tankkonstruktionen erzeugt ein Laufrad am Boden Turbulenzen, die dazu beitragen, dass Blasen und Partikel kollidieren; Die Blasen steigen durch eine Ruhezone auf und sammeln sich oben in einer Schaumschicht.
Graeme Jameson, Laureate Professor an der Universität von Newcastle in Australien, erklärte, dass, wenn Partikel an Blasen hängen, die sich in Flüssigkeitswirbeln mit 100 Umdrehungen pro Sekunde drehen, es eine kritische Größe gibt, bei der sich ein Partikel einfach von der Blase löst.
Hochenergetische Turbulenz eignet sich hervorragend für die Rückgewinnung kleiner Partikel, und die Existenz von Turbulenzen ist es, die Partikel aller Größen in Suspension hält. Aber diese Turbulenz hält auch grobe Partikel vom Schweben ab.
„Je gröber die Partikel sind, desto schneller müssen Sie die Flüssigkeit umrühren, um sie vom Boden des Gefäßes fernzuhalten“, sagte er. „Es ist also ein selbstzerstörerisches Gerät, wenn man versucht, grobe Partikel zu schweben.“
Wirbelbetten
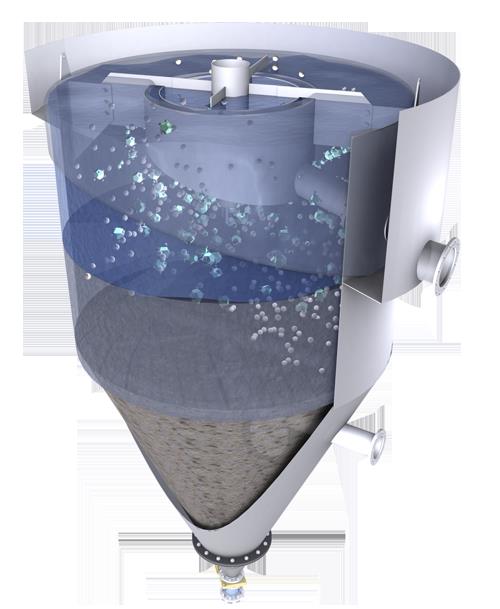
Anstelle eines Laufrads verwendet der HydroFloat von Eriez ein Wirbelbett, um grobe Erzpartikel anzuheben. Von oben gespeist, hat das Schiff einen Wassereinlass etwa zwei Drittel des Weges nach unten. Wenn grobe Partikel auf den Boden sinken, drückt der konstante Wasserfluss sie sanft wieder nach oben und stört kontinuierlich eine Region, die zu etwa 65 Prozent aus Feststoffen besteht. Das Wasser wurde mit Druckgas und einem aufschäumenden Additiv behandelt, um Blasen zu erzeugen, an denen sich die groben Partikel anlagern können. Während mineralisierte Partikel in die Überlaufwäsche schwimmen, setzt sich grober Gang zu einer Entwässerungszone im unteren Drittel des Gefäßes ab. Wenn diese Zone eine bestimmte Dichte erreicht, wird ihr Inhalt in den Unterströmungsauslass abgegeben.
Ken Roberts, Global Sales Director bei Eriez, sagte, dass HydroFloat die Flotation bis zu 400 oder mehr Mikrometer verlängern kann. In einigen Sulfiderzen hat es Zwei-Millimeter-Partikel zurückgewonnen – das entspricht 2.000 Mikrometern. Darüber hinaus sagte er: „Wir haben durch Forschung mit der University of Utah bewiesen, dass wir ein Teilchen mit einer Oberflächenmineralisierung von zwei Prozent schweben lassen können.“
HydroFloat ist ausdrücklich nicht dazu gedacht, feine Partikel aufzuschwimmen. Die Idee ist, dass es Teil eines geteilten Kreislaufs ist, der in grob und fein sortiert ist und auf jeden zugeschnittene Technologien enthält. Die Praxis hat sich bei nichtmetallischen Erzen wie Kali und Diamanten bewährt; Eriez ist in den letzten Jahren gerade in den Metallmarkt eingebrochen.
Jameson arbeitet seit 2006 im Labor an seiner eigenen Wirbelschichtlösung. Sein Design adaptiert die gleichnamige Jameson-Zelle, die er Ende der 1980er Jahre patentieren ließ. Im Gegensatz zum HydroFloat behandelt seine Zelle fein und grob zusammen. Die Flotationszufuhr läuft zuerst an einem Luftstrahl vorbei, wo sie auf die hohe Energie trifft, die zum Anbringen feiner Partikel an Blasen nützlich ist. „Das ist wie die Jameson-Zelle“, sagte er.
Dann fließt es in ein Wirbelbett, wo sich in der energieärmeren Umgebung grobe Partikel anlagern können. Die mit Erz beladenen Blasen schwimmen zu einer Schaumschicht auf und laufen in eine Wäsche über. Eine Rückführleitung entnimmt Flüssigkeit von der Oberseite und recycelt sie in den Boden, um für die Fluidisierung verwendet zu werden. Alle feinen Partikel, die in der Recyclinglinie ausgewaschen werden, werden erneut an einer Blase in der Nähe der Basis befestigt. Feine Gangart tendiert zu einem Überlaufauslass.
Vor einem Jahr bekam Jameson ein Porphyr-Kupfererz aus Südamerika in die Hände, und seine kürzlich abgeschlossenen Testarbeiten zeigen ermutigende Ergebnisse. „Wir können eine 100-prozentige Rückgewinnung bis zu etwa 300 Mikron erreichen“, sagte er.
Jetzt sucht Jameson nach einem Minenstandort, der bereit ist, eine vollständige Installation von etwa 50 bis 100 Tonnen pro Stunde zu testen. „Der Punkt dieser Größe ist, dass die einzelne Einheit relativ einfach zu handhaben und zu bauen ist“, sagte er. „Sie können es auf einem LKW zu einer Baustelle bringen und dort installieren und Ihre Testarbeiten durchführen, und dann haben Sie etwas, von dem Sie zuverlässig skalieren können.“
Bauen Sie es größer – aber intelligenter
Obwohl bewährte Technologie das Schweben von grobem Erz unterstützt, ist dies bei weitem nicht die Norm. „Die Bergbauindustrie hat in der Vergangenheit sinkende Futtermittelgehalte und höhere Kosten durch die Nutzung von Skaleneffekten angegangen“, sagte Walter Valery, Global Director of Consulting and Technology for mining and Mineral Processing bei Hatch. Die Tendenz ist, „große Tonnagen zu behandeln, das gesamte Material fein zu mahlen und die nachgelagerten Trennprozesse alles aussortieren zu lassen. Dies ist jedoch in der Regel sehr ineffizient und während Ausfallzeiten weder verantwortlich noch praktikabel.“
Große Ausrüster erfüllen diese Nachfrage, indem sie immer größere Flotationszellen entwickeln. Vor dreißig Jahren wäre eine Zelle mit einem Volumen von 30 Kubikmetern ungewöhnlich groß gewesen. Heute sind 300-Kubikmeter-Zellen an der Tagesordnung. Outotec hat eine 500-Kubikmeter-Zelle in Betrieb und mehrere 630-Kubikmeter-Zellen in Lieferung, während FLSmidth eine 660-Kubikmeter-Zelle in Betrieb hat.
Der Bau eines großen Tanks bietet Energieeinsparungen. Das scheint besonders hell für Bergbauunternehmen, die sich neu für die Energiekosten der Flotation interessieren – früher ein Hauptthema nur in der Zerkleinerung, aber jetzt in den Fokus rücken, da der Kostendruck im Allgemeinen zunimmt und die Flotationstonnagen steigen.
„Wenn wir die Größe verdoppeln, sparen wir in der Praxis mindestens 10 bis 20 Prozent Energie“, sagt Antti Rinne, Vice President Reficiification Sales bei Outotec. „Das ist im Moment in den meisten Ländern der Welt eine riesige Menge Geld.“
Diese allmähliche Skalierung hat Nachteile. Wenn das Volumen des Tanks zunimmt, erreichen die Turbulenzen nicht unbedingt eine angemessene Höhe, was zumindest einen Teil des zusätzlichen Tankvolumens zu einer Verschwendung von Platz, Stahl und Geld macht.
„Der Anteil der Zelle, die sehr turbulent ist, hat deutlich abgenommen, da die Größe der Flotationszellen in den letzten 20 Jahren dramatisch zugenommen hat“, sagte Erico Tabosa, Minerals Processing Engineer bei Hatch.
FLSmidth hat dieses Problem durch sein neues NeXTStep-Laufraddesign gelöst, das entwickelt wurde, um „tote“ Räume ohne Turbulenzen zu beseitigen. Dadurch macht das neue Design die Maschine auch energieeffizienter. „Wir haben festgestellt, dass unsere Leistung im Vergleich zu anderen Umluft-Flotationsmaschinen konstant niedriger ist“, sagte Asa Weber, Flotation Technology Director bei FLSmidth.
Die andere wichtige Innovation von FLSmidth ist die Hybridenergieschaltungskonfiguration, die ein Problem der Inkonsistenz in Schwimmerzellen behebt. Da in jeder Zelle eines Kreislaufs etwas Erz gewonnen wird, ändern sich die mineralogischen Eigenschaften von Zelle zu Zelle, das Zelldesign selbst jedoch nicht.
Outotec entwickelte auch Möglichkeiten zur Skalierung bei gleichzeitiger Aufrechterhaltung der Energieeffizienz. Seine eigenen neuartigen Laufraddesigns, die 2007 eingeführt wurden, umfassen einen Rotor / Stator mit ähnlichen turbulenzverteilenden Vorteilen, genannt FloatForce. Outotec erfand auch ein Hilfslaufrad namens FlowBooster, das die Durchmischung im Tank mit sehr geringer zusätzlicher Energie weiter verbessert.
Es wurden erhebliche Anstrengungen unternommen, um die beste Laufraddrehzahl für das spezifische Erz und die Anwendung zu finden. „Wir haben in den letzten Jahren viel an drehzahlvariablen Antrieben für Flotationszellen gearbeitet“, sagte Ben Murphy, Technology Director of Flotation bei Outotec. Die ersten großen Zellen, die mit einem drehzahlgeregelten Antrieb betrieben werden, wurden vor etwa fünf Jahren installiert. Seitdem haben solche Anlagen gezeigt, dass sie den Energieverbrauch, die Rückgewinnung oder manchmal sogar beides maximieren können.
„Das Interessante ist, dass wir tatsächlich in der Lage waren, einen Großteil der Geschwindigkeitsoptimierung und der Arbeit zur Energieeinsparung auf kleine Zellen zu reduzieren“, fügte Murphy hinzu. „Was irgendwie ordentlich ist; es funktioniert nicht immer so.“ Für einen kleinen Betrieb, der auf Dieselgeneratoren an einem abgelegenen Ort angewiesen ist, könnte das echtes Geld sparen.
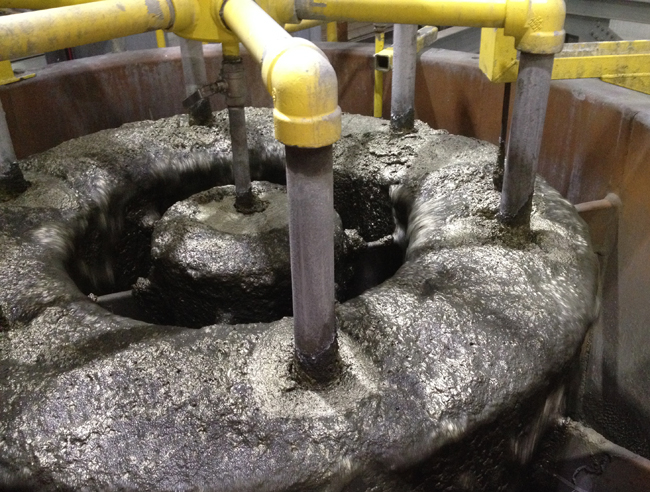
Separate Kammern
Barrick verwendet in seinen Betrieben große konventionelle Zellen. Es arbeitet aber auch mit verschiedenen Konsortien zusammen, um „die nächste Generation“ effizienterer Flotationsmaschinen zu entwickeln, so Gorain. „Skaleneffekte funktionieren immer noch für einige Erze, aber für niedriggradige komplexe Erzkörper nähern sich diese konventionellen Zellen ihren technischen Grenzen oder ihre Vorteile sind bestenfalls marginal“, sagte er.
Das Konsortium förderte die Arbeit an einem neuen Design von Woodgrove Technologies. Anstelle von getrennten Zonen in einem Behälter teilt der Stufenflotationsreaktor (SFR) den Flotationsprozess in drei Kammern auf: eine turbulente Partikelsammeleinheit, eine ruhende Blasenauslöseeinheit und eine ähnlich ruhende Schaumrückgewinnungseinheit. Jeder SFR wird für die projizierten Erzeigenschaften jeder Mine maßgeschneidert.
„Wir betrachten den Gehalt und die Tonnage über die Lebensdauer der Mine und entwerfen dann die Schaumrückgewinnungseinheit, um die gewichtete Verteilung der Metalleinheiten über diesen Zeitraum zu steuern“, sagte Glenn Kosick, Präsident von Woodgrove Technologies. „Wenn Sie sich beispielsweise am hinteren Ende einer Bank von Standard-Flotationsmaschinen befinden, entfernen Sie möglicherweise 0,3 bis 0,5 Tonnen pro Stunde und Quadratmeter. Mit dieser Maschine können Sie mit 2,5 bis drei Tonnen pro Stunde und Quadratmeter arbeiten.“
Kosick sagte, dass das effiziente Design des SFR seinen Energieverbrauch im Vergleich zu einer herkömmlichen Flotationszelle fast halbiert und die begrenzte Nutzung der Bodenfläche die Installation billiger macht. „Wir haben es auf die Reduzierung der Kapital- und Betriebskosten verkauft“, sagte er. Sein Design fördert aber auch eine bessere Selektivität aufgrund der großen Reduzierung der in diesen Maschinen verwendeten Luft im Vergleich zu Tankzellen.
„Die Daten, die wir in vollem Umfang zurückerhalten, zeigen uns, dass wir gröberes Material durch Einschränkung der Oberfläche aufschwimmen können, was zu sehr stabilen Schäumen und kurzen Transportwegen führt“, sagte Kosick. Die gröbste Zelle, die jetzt arbeitet, läuft bei einem Vorschub p80 von etwa 230 Mikron; die feinste liegt bei 20 Mikron.
Zweiundzwanzig SFR sind seit 2010 in Betrieb gegangen; mehr als 130 sind in Planung. Nach einigen erfolgreichen Installationen in kleinen Minen finanzierte das Konsortium einen Versuchsmaßstab von bis zu 930 Tonnen pro Stunde in der Kupfermine Sossego von Vale in Brasilien. Eines der Konsortialunternehmen hat Woodgrove kürzlich mit dem detaillierten Engineering für eine Installation in einem 95.000 Tonnen pro Tag schweren Kupferprojekt in Chile beauftragt.
Kombinationslösungen
Diese neuen Lösungen werden häufig als eigenständige Projekte vorgestellt und können installiert werden. Aber sie sind am effektivsten, wenn sie ganzheitlich gesehen werden. So fusionierte Woodgrove kürzlich mit dem Prozesssteuerungslieferanten Portage Technologies, um Ausrüstung und Prozessüberwachung als ein Paket zu liefern. Woodgrove kann jetzt ein Schaumcharakterisierungssystem anbieten, um Schaumgeschwindigkeit, Stabilität und Farbe zu messen; und Blasengröße, Anzahl und Dichte, und es kann rechtzeitig Vorschläge für Änderungen an den Geräteeinstellungen machen. Darüber hinaus kann die Vorschleif- und Zyklonsteuerung Stöße stabilisieren und verhindern, dass Gesteine den Flotationskreislauf erreichen.
In größerem Maßstab sind innovative Flussdiagrammdesigns und Reagenzienschemata ebenso wichtig wie der Bedarf an effizienten Flotationsgeräten. Zum Beispiel verwendet Barrick sein eigenes patentiertes Flussdiagramm für einen sehr komplexen feuerfesten Golderzkörper. Der Prozess („Mühle-Chemie-Schwimmer-Mühle-Chemie-Schwimmer“) beinhaltet das Aufschwimmen der gröberen Partikel in der Zufuhr zuerst, Nachschleifen und dann das Aufschwimmen der Feinstoffe, jedoch mit geeigneter Chemie, um das Grobgut und die Feinstoffe getrennt voneinander anzupassen.
Die Berater von Hatch schlagen, wie viele, die in Forschung und Innovation tätig sind, vor, ein auf einen bestimmten Satz von Erzkörpern zugeschnittenes Flussdiagramm von Mine zu Mühle zu verwenden.
Ein neu erfundenes Flussdiagramm kann mit gezielterem Strahlen beginnen; es kann Flotation mit Mahlen durchsetzen. Kristy Duffy, ein Mineralverarbeitungsingenieur bei Hatch, schlug vor, dass die neuen groben Flotationstechnologien in einer Vorkonzentrationsstufe nützlich sein könnten, um groben Gang zu entfernen. Die Stufen können laufen: Grobmahlung, Vorkonzentrationsflotation, Mahlen, rauere Flotation, Mahlgut und Reinigungsflotation.
Gorain stimmt zu, dass es möglicherweise von Nutzen sein könnte. „Nicht-flotationsbasierte Vorkonzentration ist eigentlich viel attraktiver, weil Sie versuchen, mit dem Abfall direkt im Bergbau umzugehen, bevor eine größere energieintensive Zerkleinerung verfolgt wird“, sagte er. Wenn jedoch die Erzmineralogie für andere Methoden zu weit und zu fein verbreitet ist, dann glaubt er, dass die Flotation möglicherweise ein effektiver erster Konzentrationsschritt sein könnte.
Ein breiteres Interesse richtet sich auf die Erzsortierung, die dazu beitragen kann, Gangbildung frühzeitig zu beseitigen, und die in den Diskussionen zwischen Mine und Mühle eine wichtige Rolle spielt. Roberts von Eriez sagte, dass mehrere Majors es Hand in Hand mit einer möglichen HydroFloat-Installation untersuchten.
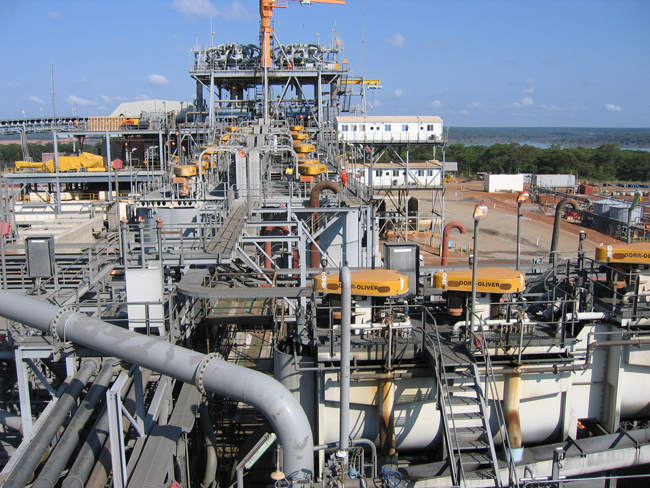
Die Auswirkungen des Abschwungs
Die anhaltenden finanziellen Schwierigkeiten der Branche in den letzten Jahren haben die Innovation vorangetrieben, da viele Projekte ohne neue Ansätze einfach nicht realisierbar wären. „Ich habe mich vor ungefähr einem Monat mit zwei Majors getroffen, die in einem Joint Venture in Südamerika tätig sind, und ihnen nicht nur den HydroFloat gezeigt, sondern auch eine andere Technologie, die wir haben“, sagte Roberts. „Und das war der springende Punkt des Treffens: ‚Sag uns, was du hast, das ist neu. Vor fünf, zehn Jahren würde das noch niemand sagen.“
Woodgrove Technologies beschäftigt sich auch während des Abschwungs – ohne sich selbst vermarkten zu müssen, so Kosick. „Wir stellen hier fast wöchentlich ein, um mit der Nachfrage Schritt zu halten“, sagte er.
Der Abschwung hat aber auch die Forschung erstickt, die neue Innovationen hervorbringen könnte. „Die meisten R & D-Abteilungen von Unternehmen sind vom Abschwung im Bergbau stark betroffen“, sagte Sergio Vianna, ein Minerals Processing Engineer bei Hatch. „Daher gibt es in den letzten Jahren kaum neue Lösungen in der Mineralaufbereitung.“
Um die Größe und Auswahl herkömmlicher Zellen zu erleichtern, möchte Hatch eine detaillierte Studie darüber durchführen, mit welcher Geschwindigkeit Schaum die zurückgewonnenen Mineralien stabil über die Lippe der Schwimmzelle transportieren kann. Aber Vianna hat Zweifel, dass eine solche Studie im aktuellen Forschungsklima stattfinden kann.
Kym Runge, Principal Research Fellow am Julius Kruttschnitt Mineral Research Centre (JKMRC) an der University of Queensland in Australien, ist besorgt, dass Australiens ehemals gesundes Ökosystem aus Forschungszentren, Minenstandorten und Beratungsunternehmen bei anhaltenden Trends in Gefahr ist, zu weit zurückgeschnitten zu werden. Viele weltweit führende Unternehmen in der Mineralverarbeitung haben JKMRC durchlaufen oder verwenden dort entwickelte Werkzeuge.
Aber die Forschung geht weiter, wo sie kann. „Wir haben viele andere Technologien, an denen wir arbeiten“, sagte Gorain von Barrick. „Natürlich sind sie streng vertraulich, daher können wir nicht darüber sprechen. Im Allgemeinen geht es jedoch darum, Lösungen für verschiedene komplexe Erzkörper zu entwickeln.“
Runge arbeitet an einer Reihe von Forschungsprojekten. Trotz der Fortschritte der Gerätehersteller glaubt sie, dass es viel mehr zu verstehen gibt, wie Turbulenzen die Flotation in den größeren Zellen beeinflussen. „Viele Leute haben gerade eine Variable geändert und Korrelationen gesehen und daraus Schlussfolgerungen gezogen“, sagte sie.
Sie sieht auch die Notwendigkeit, die Art des integrierten, neuartigen Flussschemas zu simulieren, das am JKMRC vorgesehen ist. „Weil sie risikoarme Bestien sind, die Bergbauindustrie“, sagte sie, „also in der Lage zu sein, zu bewerten,“Was wird der wirtschaftliche Vorteil sein, eine Grobpartikel-Flotationseinheit in die Mitte meines Mahlens zu stellen?‘ wird es ermöglichen, dass das angenommen wird.“
Auf die Frage, wie Flotationskreisläufe in zehn Jahren aussehen würden, zeigte sich Runge konservativ optimistisch. „Ich hoffe, dass wir sehen werden, wie einige dieser neuen Technologien eingeführt werden“, sagte sie. „Ich weiß, dass wir höhere Durchsätze behandeln werden. Und so müssen sie größer werden, aber hoffentlich werden wir auch anfangen, die Dinge ein wenig schlauer zu machen.“