Come criteri di progettazione, rimuovere lo strato di schiuma dalla flottazione della schiuma rende una dichiarazione audace. Il fatto che un tale dispositivo non solo esista, ma abbia 50 installazioni operative, testimonia la pressione sull’industria per trovare nuove soluzioni di fronte alle sfide moderne. Bassi gradi, minerali complessi e costi energetici crescenti hanno spinto lo sviluppo di navi di galleggiamento completamente nuove, miglioramenti alla tecnologia esistente e nuove riflessioni sui fogli di flusso di galleggiamento.
La nave di galleggiamento senza schiuma proviene dalla Eriez Flotation Division, che l’ha brevettata nel 2002 e commercializzata con il nome HydroFloat. È destinato specificamente a un flowsheet innovativo che affronta uno dei maggiori problemi che le operazioni minerarie devono affrontare: con più tonnellaggi da elaborare e più minerale a grana fine, la sminuzzatura richiede sempre più energia. Se i circuiti di flottazione sono in grado di gestire particelle più grossolane, l’energia potrebbe essere salvata nel circuito di comminuzione.
“La maggior parte delle società minerarie si occupa di declinare i gradi di minerale e la mineralogia complessa”, ha affermato Barun Gorain, direttore del Strategic Technology Solutions Group di Barrick Gold. “Il vero problema è che più del 99% di ciò che effettivamente estraggiamo nell’industria dell’oro è considerato spreco.”Ha detto che la flottazione di particelle grossolane potrebbe consentire alle miniere di rifiutare alcuni rifiuti all’inizio della catena del valore, il che contribuirà a ridurre i costi di capitale e operativi.
Sfortunatamente, la cella di flottazione convenzionale raggiunge un elevato recupero solo in intervalli di dimensioni limitati. Ad esempio, un minerale di solfuro potrebbe galleggiare molto bene a 90 a 120 micron, ma non a 50 o 150 micron.
La ricerca finora ha identificato due ragioni principali per il limite superiore delle dimensioni delle particelle fluttuanti. Innanzitutto, le particelle più grossolane tendono a non avere la stessa mineralizzazione superficiale per attirare le bolle.
In secondo luogo, anche se sono in grado di attaccarsi, tendono a staccarsi di nuovo. Nella maggior parte dei progetti di serbatoi convenzionali, una girante nella parte inferiore crea turbolenza che aiuta le bolle e le particelle a scontrarsi; le bolle salgono attraverso una zona di riposo e si riuniscono in uno strato di schiuma nella parte superiore.
Graeme Jameson, professore laureato presso l’Università di Newcastle in Australia, ha spiegato che se le particelle sono appesi a bolle che girano in vortici liquidi a 100 giri al secondo, c’è qualche dimensione critica in cui una particella si staccherà semplicemente dalla bolla.
La turbolenza ad alta energia è ottima per il recupero di piccole particelle e, in base alla progettazione, l’esistenza della turbolenza è ciò che mantiene particelle di tutte le dimensioni in sospensione. Ma quella turbolenza scoraggia anche le particelle grossolane dal galleggiare.
“Più grossolane sono le particelle che hai, più velocemente devi mescolare il liquido per tenerle lontane dal fondo della nave”, ha detto. “Quindi è un pezzo di equipaggiamento controproducente dal punto di vista del tentativo di galleggiare particelle grossolane.”
Letti fluidi
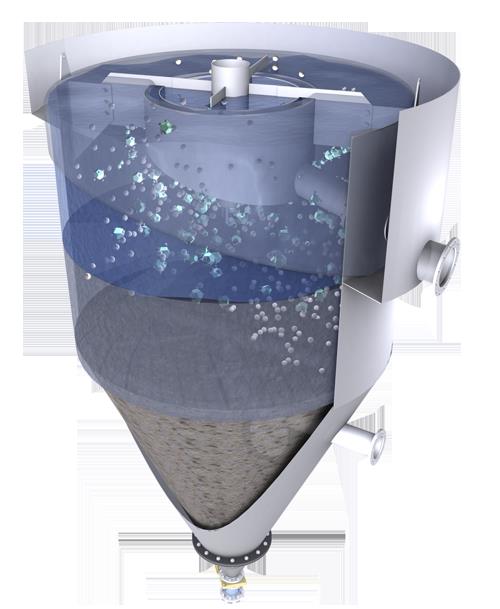
Invece di una girante, l’HydroFloat di Eriez utilizza un letto fluidizzato per sollevare particelle di minerale grossolano. Alimentato dall’alto, la nave ha una presa d’acqua a circa due terzi della discesa. Come particelle grossolane affondano verso il basso, il flusso costante di acqua li spinge delicatamente indietro, interrompendo continuamente una regione che è di circa 65 per cento solidi. L’acqua è stata trattata con gas compresso e un additivo schiumogeno per generare bolle a cui le particelle grossolane possono attaccarsi. Mentre le particelle mineralizzate galleggiano nella lavanderia a troppopieno, la ganga grossolana si deposita in una zona di disidratazione nel terzo inferiore della nave. Quando quella zona raggiunge una certa densità, il suo contenuto viene rilasciato nell’uscita underflow.
Ken Roberts, Global Sales Director di Eriez, ha affermato che HydroFloat può estendere la flottazione fino a 400 o più micron. In alcuni minerali di solfuro, ha recuperato particelle di due millimetri-traducendosi in 2.000 micron. Inoltre, ha detto, ” Abbiamo dimostrato con la ricerca con l’Università dello Utah che possiamo galleggiare una particella con mineralizzazione superficiale del due per cento.”
HydroFloat non è esplicitamente destinato a galleggiare particelle fini. L’idea è che sarebbe parte di un circuito split, presorted in grossolana e fine, con tecnologie su misura per ciascuno. La pratica è stata dimostrata in minerali non metallici come potassio e diamanti; Eriez è stato appena rotto nel mercato dei metalli negli ultimi due anni.
Jameson lavora in laboratorio sulla propria soluzione a letto fluido dal 2006. Il suo design adatta l’omonima cellula Jameson che ha brevettato alla fine degli anni ‘ 80. In contrasto con l’HydroFloat, la sua cellula tratta bene e grossolana insieme. L’alimentazione di flottazione passa prima da un getto d’aria, dove incontra l’alta energia utile per attaccare particelle fini alle bolle. “È come la cella di Jameson, in realtà”, ha detto.
Quindi scorre in un letto fluido, dove l’ambiente a bassa energia consente alle particelle grossolane di attaccarsi. Le bolle cariche di minerale galleggiano fino a uno strato di schiuma e traboccano in una lavanderia. Una linea di riciclo toglie il liquido dalla parte superiore e lo ricicla nella base da utilizzare per la fluidizzazione. Eventuali particelle fini lavate nella linea di riciclo ottenere un altro andare a fissare ad una bolla vicino alla base. Fine ganga tende verso una presa di troppo pieno.
Un anno fa, Jameson ha messo le mani su un minerale di rame porfido proveniente dal Sud America, e il suo lavoro di test recentemente completato mostra risultati incoraggianti. “Possiamo ottenere il recupero del 100% fino a circa 300 micron”, ha affermato.
Ora Jameson è alla ricerca di un sito minerario disposto a provare un’installazione su vasta scala di circa 50-100 tonnellate all’ora. “Il punto di quella dimensione è che la singola unità è ragionevolmente facile da gestire e da costruire”, ha affermato. “Puoi portarlo in un sito su un camion e installarlo lì e fare il tuo lavoro di test, e poi hai qualcosa da cui puoi scalare in modo affidabile.”
Costruire più grande-ma più intelligente
Anche se la tecnologia collaudata supporta galleggiante minerale grezzo, che non è affatto vicino alla norma. “L’industria mineraria ha una storia di affrontare il calo dei gradi di mangime e dei costi più elevati sfruttando le economie di scala”, ha dichiarato Walter Valery, Global Director of consulting and Technology for mining and mineral processing di Hatch. La tendenza è quella di ” trattare grandi tonnellaggi, macinare tutto il materiale finemente e lasciare che i processi di separazione a valle risolvano tutto. Tuttavia, questo è generalmente molto inefficiente e non è né responsabile né praticabile durante i tempi di inattività.”
I principali fornitori di apparecchiature soddisfano questa richiesta progettando celle di galleggiamento sempre più grandi. Trent’anni fa, una cella di 30 metri cubi di volume sarebbe stata insolitamente grande. Ora, celle di 300 metri cubi sono all’ordine del giorno. Outotec ha una cella di 500 metri cubi in funzione e diverse celle di 630 metri cubi in consegna, mentre FLSmidth ha una cella di 660 metri cubi in funzione.
La costruzione di un grande serbatoio fornisce economie di scala energetiche. Ciò brilla particolarmente per le società minerarie recentemente interessate al costo energetico della flottazione – in precedenza un tema importante solo nella sminuzzazione, ma ora si sta concentrando poiché le pressioni sui costi generalmente si intensificano e i tonnellaggi di flottazione aumentano.
“Quando raddoppiamo le dimensioni , scendiamo di almeno il 10-20 per cento di energia nella pratica”, ha affermato Antti Rinne, vicepresidente delle vendite di beneficiation di Outotec. “Questa è un’enorme quantità di denaro nella maggior parte dei paesi del mondo al momento.”
Che graduale scale-up viene fornito con aspetti negativi. Se il volume del serbatoio aumenta, la turbolenza non raggiungerà necessariamente un’altezza commisurata, il che rende almeno una parte del volume extra del serbatoio uno spreco di spazio, acciaio e denaro.
“La proporzione della cellula che è altamente turbolenta è diminuita significativamente mentre la dimensione delle celle di galleggiamento è aumentata drammaticamente durante gli ultimi 20 anni,” ha detto Erico Tabosa, ingegnere di elaborazione dei minerali a Hatch.
FLSmidth ha affrontato questo problema attraverso il suo nuovo design della girante NeXTSTEP, che è stato sviluppato per eliminare gli spazi “morti” senza turbolenze. Di conseguenza, il nuovo design rende anche la macchina più efficiente dal punto di vista energetico. “Abbiamo scoperto che siamo costantemente più bassi in potenza rispetto ad altre macchine di flottazione ad aria forzata”, ha dichiarato Asa Weber, flotation technology Director di FLSmidth.
L’altra grande innovazione di FLSmidth è la sua configurazione del circuito energetico ibrido, che risolve un problema di incoerenza nelle celle float. Poiché alcuni minerali vengono recuperati in ogni cella di un circuito, le caratteristiche mineralogiche stanno cambiando da cellula a cellula, ma il design cellulare stesso non lo è.
Outotec ha anche sviluppato modi per scalare mantenendo l’efficienza energetica. I suoi nuovi progetti di giranti, introdotti nel 2007, includono un rotore/statore con benefici simili per la distribuzione della turbolenza, chiamato FloatForce. Outotec ha anche inventato una girante ausiliaria, chiamata FlowBooster, che migliora ulteriormente la miscelazione nel serbatoio con un’energia aggiuntiva molto bassa.
È stato compiuto uno sforzo significativo per trovare la migliore velocità della girante per il minerale e l’applicazione specifici. “Negli ultimi anni abbiamo lavorato molto sugli azionamenti a velocità variabile sulle celle di flottazione”, ha dichiarato Ben Murphy, Technology Director of flotation di Outotec. Le prime grandi celle che eseguono operazioni con un azionamento a velocità variabile sono state installate circa cinque anni fa. Da allora tali installazioni hanno dimostrato di poter massimizzare l’uso di energia, il recupero o talvolta anche entrambi.
“La cosa interessante è che siamo stati in grado di drill-down un sacco di ottimizzazione della velocità e il lavoro di riduzione di energia a piccole cellule,” ha aggiunto Murphy. “Che è un po’ pulito; non sempre funziona in questo modo.”Per una piccola operazione basandosi su generatori diesel in una posizione remota, che potrebbe risparmiare denaro reale.
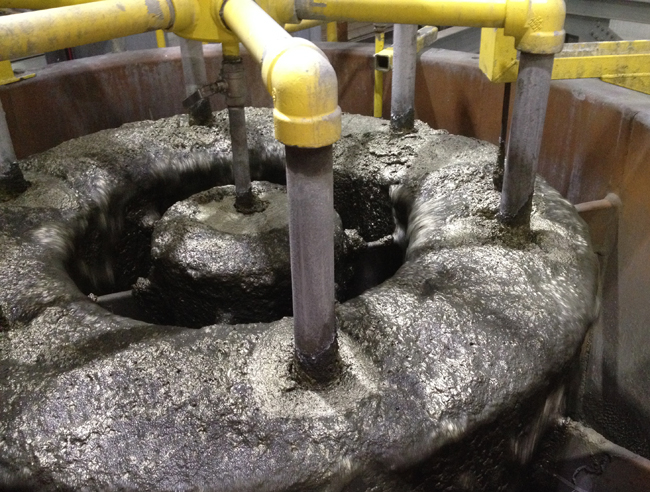
Camere separate
Barrick utilizza grandi celle convenzionali nelle sue operazioni. Ma sta anche lavorando con diversi consorzi per sviluppare “la prossima generazione” di macchine di flottazione più efficienti, secondo Gorain. “Le economie di scala funzionano ancora per alcuni minerali, ma per i corpi minerali complessi di basso grado, queste cellule convenzionali si stanno avvicinando ai loro limiti tecnici o i loro benefici sono solo marginali nel migliore dei casi”, ha affermato.
Il consorzio ha sponsorizzato il lavoro su un nuovo design di Woodgrove Technologies. Invece di zone separate in un recipiente, il reattore di flottazione staged (SFR) divide il processo di flottazione in tre camere: un’unità di raccolta delle particelle turbolente, un’unità di disinnesto delle bolle quiescenti e un’unità di recupero della schiuma allo stesso modo quiescente. Ogni SFR è costruito su misura per le caratteristiche del minerale proiettate di ogni miniera.
“Esaminiamo il grado e il tonnellaggio durante la vita della miniera, e quindi progettiamo l’unità di recupero della schiuma per gestire la distribuzione ponderata delle unità metalliche in questo periodo”, ha dichiarato Glenn Kosick, presidente di Woodgrove Technologies. “Ad esempio, se sei sul retro di una banca di macchine di flottazione standard, potresti rimuovere da 0,3 a 0,5 tonnellate all’ora per metro quadrato. Mentre con questa macchina, potresti funzionare da 2,5 a tre tonnellate all’ora per metro quadrato.”
Kosick ha detto che il design efficiente di SFR riduce il suo uso di energia quasi a metà rispetto a una cella di flottazione convenzionale, e il suo uso limitato di spazio sul pavimento lo rende più economico da installare. “Lo abbiamo venduto sulla riduzione del capitale e dei costi operativi”, ha affermato. Ma il suo design promuove anche una migliore selettività grazie alle grandi riduzioni di aria utilizzate in queste macchine rispetto alle celle del serbatoio.
“I dati che stiamo ottenendo a fondo scala ci mostrano che possiamo galleggiare materiale più grossolano limitando l’area superficiale, il che si traduce in schiume molto stabili e brevi distanze di trasporto”, ha affermato Kosick. La cella più grossolana che funziona ora funziona con un feed p80 di circa 230 micron; la più bella è a 20 micron.
Ventidue SFRS sono entrati in funzione dal 2010; più di 130 sono in fase di progettazione. Dopo alcune installazioni di successo in piccole miniere, il consorzio ha finanziato una scala di prova-fino a 930 tonnellate all’ora nella miniera di rame di Sossego in Brasile. Una delle società del consorzio ha recentemente assegnato a Woodgrove l’ingegneria di dettaglio per un’installazione in un progetto di rame da 95.000 tonnellate al giorno in Cile.
Soluzioni combinate
Queste nuove soluzioni sono spesso presentate e possono essere installate come progetti discreti. Ma sono più efficaci se visti olisticamente. Ad esempio, Woodgrove si è recentemente fusa con il fornitore di controllo di processo Portage Technologies, consentendo all’it di fornire apparecchiature e monitoraggio dei processi come un unico pacchetto. Woodgrove può ora offrire un sistema di caratterizzazione della schiuma per misurare la velocità della schiuma, la stabilità e il colore; e la dimensione della bolla, il conteggio e la densità, e può fornire suggerimenti tempestivi per le modifiche alle impostazioni delle apparecchiature. Inoltre, la sua rettifica in anticipo e il controllo del ciclone possono stabilizzare i picchi e impedire alle rocce di raggiungere il circuito di galleggiamento.
Su scala più ampia, progetti innovativi di flowsheet e schemi di reagenti sono altrettanto importanti quanto la necessità di apparecchiature di flottazione efficienti. Ad esempio, Barrick sta utilizzando il proprio foglio di flusso brevettato per un corpo di minerale d’oro refrattario molto complesso. Il processo (“Mill-Chemistry-Float-Mill-Chemistry-Float”) comporta prima il galleggiamento delle particelle più grossolane nel mangime, la riaffilatura e poi il galleggiamento delle multe, ma abilitato con una chimica appropriata per adattarsi separatamente alle grossolane e alle multe.
I consulenti di Hatch, come molti che lavorano sulla ricerca e l’innovazione, suggeriscono di adottare un design del flowsheet da miniera a mulino su misura per un particolare insieme di corpi minerari.
Un foglio di flusso reinventato potrebbe iniziare con una sabbiatura più mirata; potrebbe intercalare la flottazione con la rettifica. Kristy Duffy, un ingegnere di lavorazione dei minerali a Hatch, ha suggerito che le nuove tecnologie di flottazione grossolana potrebbero essere utili in una fase di pre-concentrazione per rimuovere la ganga grossolana. Le fasi possono essere eseguite: macinatura grossolana, flottazione pre-concentrazione, macinatura, flottazione più ruvida, riaffilatura e flottazione di pulizia.
Gorain concorda sul fatto che potrebbe potenzialmente essere utile. “La pre-concentrazione non basata sulla flottazione è in realtà molto più attraente, perché si sta cercando di affrontare i rifiuti proprio nell’estrazione prima che venga perseguita qualsiasi grande comminuzione ad alta intensità energetica”, ha affermato. Tuttavia, se la mineralogia del minerale è troppo ampiamente e finemente diffusa per altri metodi, allora pensa che la flottazione potrebbe potenzialmente essere un primo passo di concentrazione efficace.
L’interesse più diffuso è diretto verso lo smistamento del minerale, che può aiutare a eliminare il ganga nella fase iniziale e presenta un forte impatto nelle discussioni tra miniere e mulini. Roberts di Eriez ha detto che diverse major stavano indagando mano nella mano con una potenziale installazione di HydroFloat.
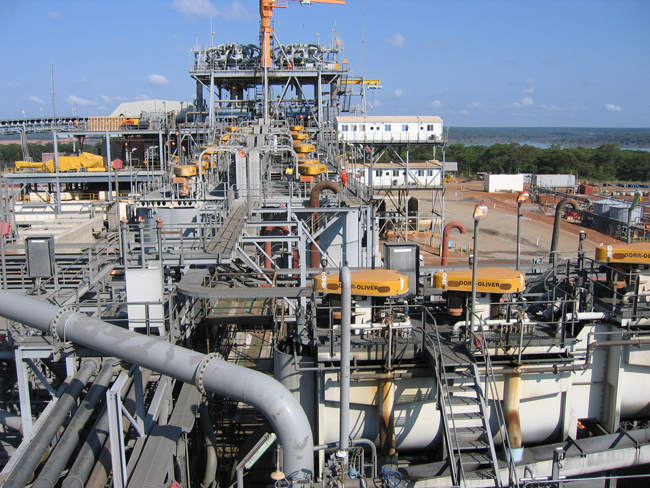
Gli effetti della recessione
Gli ultimi anni di prolungate difficoltà finanziarie per l’industria hanno costretto alcuni movimenti in avanti sull’innovazione, poiché molti progetti semplicemente non sarebbero praticabili senza nuovi approcci. “Ho incontrato due major che sono in una joint venture in Sud America probabilmente circa un mese fa e ha mostrato loro non solo l’HydroFloat, ma qualche altra tecnologia che abbiamo”, ha detto Roberts. “E questo è stato il punto centrale dell’incontro: ‘Dicci cosa hai che è nuovo. Cinque, dieci anni fa, nessuno l’avrebbe mai detto.”
Woodgrove Technologies è anche tenere occupato durante la crisi – senza dover commercializzare se stesso, secondo Kosick. “Stiamo assumendo quasi settimanalmente qui per cercare di tenere il passo con la domanda”, ha detto.
Ma la crisi ha anche soffocato la ricerca che potrebbe produrre nuove innovazioni. “La maggior parte delle divisioni R&D delle aziende sono state gravemente colpite dalla crisi mineraria”, ha affermato Sergio Vianna, ingegnere di lavorazione dei minerali di Hatch. “Pertanto, ci sono un numero scarso di nuove soluzioni sviluppate nella lavorazione dei minerali negli ultimi anni.”
Per aiutare a dimensionare e selezionare le celle convenzionali, Hatch vorrebbe avere uno studio dettagliato sulla velocità con cui la schiuma può trasportare stabilmente i minerali recuperati sul labbro della cella galleggiante. Ma Vianna ha dubbi sul fatto che un tale studio possa accadere nell’attuale clima di ricerca.
Kym Runge, research fellow principale presso il Julius Kruttschnitt Mineral Research Centre (JKMRC) presso l’Università del Queensland in Australia, è preoccupato che l’ecosistema precedentemente sano dell’Australia di centri di ricerca, siti minerari e consulenze rischia, se le tendenze continuano, di essere tagliato troppo lontano per tornare indietro. Molti leader mondiali nella lavorazione dei minerali sono passati attraverso JKMRC o utilizzano strumenti sviluppati lì.
Ma la ricerca continua dove può. “Abbiamo molte altre tecnologie su cui stiamo lavorando”, ha detto Gorain di Barrick. “Ovviamente sono altamente confidenziali, quindi non saremo in grado di parlarne. Ma in generale, l’idea è quella di sviluppare soluzioni per vari corpi minerali complessi.”
Runge sta lavorando a una serie di progetti di ricerca. Nonostante i progressi compiuti dai produttori di apparecchiature, pensa che ci sia molto di più da capire su come la turbolenza influisce sulla flottazione nelle cellule più grandi. “Molte persone hanno appena cambiato una variabile e hanno visto correlazioni e ne hanno tratto conclusioni”, ha detto.
Vede anche la necessità di simulare il tipo di flowsheet integrato e innovativo previsto da JKMRC. “Perché sono bestie a basso rischio, l’industria mineraria”, ha detto, “quindi essere in grado di valutare” Quale sarà il vantaggio economico di mettere un’unità di flottazione di particelle grossolane nel mezzo della mia macinatura?”consentiranno di adottarlo.”
Alla domanda su come sarebbero stati i circuiti di flottazione tra dieci anni, Runge era conservativamente ottimista. “Spero che inizieremo a vedere alcune di queste nuove tecnologie iniziare ad essere adottate”, ha detto. “So che tratteremo produzioni più elevate. E così avranno bisogno di diventare più grandi, ma speriamo che inizieremo anche a fare le cose un po ‘ più intelligenti.”